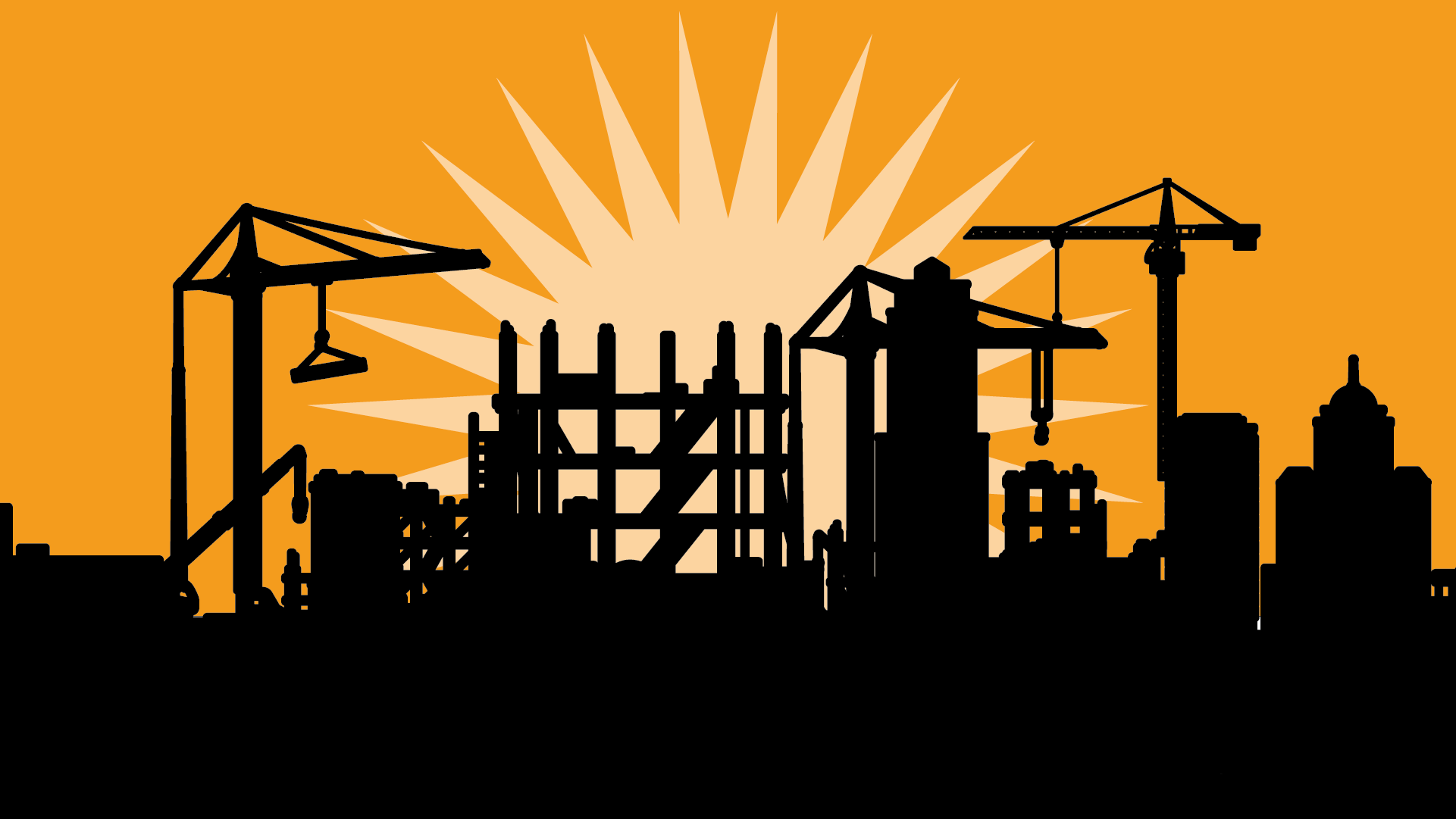
Toolbox Talks
Toolbox Talks safety briefings are an easy and efficient way to keep your construction worker employees safe.
What are Toolbox Talks?
These brief meetings offer an opportunity for team members to learn about potential hazards and preventive measures, as well as a chance for the employer to review safety regulations. They are a great way to ensure that everyone is aware of the safety protocols that must be adhered to in order to prevent accidents and injuries on the job site.
NEW! Search Toolbox Talks
Type a search term in the search box below to view English toolbox talks that match your search query. Or, use the category dropdown to view related talks.
Cutting and Welding
Date Posted: 09/19/2016
Welding and cutting pose several hazards on the jobsite. Following proper guidelines and wearing appropriate attire, you can eliminate the possibility of an accident.
Demolition Safety
Date Posted: 09/18/2016
Demolition is high-risk work and adequate preparations are required. Falls and premature collapse of structures are the greatest risk. Communication is the best line of defense to reduce injury.
Diesel Exhaust
Date Posted: 09/18/2016
Diesel engines provide power to a wide variety of vehicles, heavy equipment and machinery in a large number of industries such as construction, transportation, mining, agriculture and types of manufacturing operations.
Driver Safe Work Zone
Date Posted: 09/18/2016
Unexpected traffic delays can be avoided by following specific guidelines at the Traffic Control Zone.
Drywall Installing Safety
Date Posted: 09/17/2016
Workers who handle drywall sheets are at high risk of overexertion and fall injuries. Drywall installers spend most of the day standing, bending, or stretching. This work is physically demanding.
Electrical Ground Safety
Date Posted: 09/17/2016
It is critical to understand where electricity is located on a jobsite in order to avoid electrocutions of electrical workers.
Electric Powertools and Cords
Date Posted: 09/16/2016
Use only electrical equipment that is approved for use in the workplace and for the type of work to be performed. The use of approved equipment does not eliminate all dangers if the equipment is damaged or is used in adverse conditions, such as in rain or wet areas.
Excavations and Trenches
Date Posted: 09/16/2016
Not everyone on a given project is directly involved with trenching. However, many people work near trenches and excavations. Excavation safety is not just for workers in the hole. If you observe an unsafe act, stop work and save someone’s life. (WAC 296-155 Part N)
Exit Route Safety
Date Posted: 09/15/2016
An exit route is a continuous and unobstructed path from any point within a workplace to a place of safety.
Extension Ladder Safety
Date Posted: 09/15/2016
Ladders are probably the most used and misused piece of access and egress equipment and their usage accounts for a large percentage of accidents. Keep attention to details when working with ladders. Ensure that you choose a ladder that is tall enough for you to safely access your work area or reach your task. The ladder must also be strong enough to support you and your tools, and suitable for your work environment.
Fall Protection
Date Posted: 09/15/2016
Falls are the most frequent cause of fatalities in construction and annually account for one of every three construction-related deaths. Fall protection trigger heights will vary depending on the task being performed. The “trigger height” is the minimum height at which fall protection is required. Know the trigger heights for your work and use fall protection as required.
Fire Extinguisher Systems and Maintenance
Date Posted: 09/14/2016
Using the proper fire extinguisher is extremely important and the use of the wrong type may actually spread the fire. All fire extinguishers have a label to tell you what fires they can extinguish.
Fire Prevention
Date Posted: 09/14/2016
When workers think of fire prevention, they often think of fire extinguishers and having them close by to prevent a larger fire. When fire prevention is done right, it eliminates the need of a fire extinguisher.
First Aid
Date Posted: 09/13/2016
The priorities of first aid are to; save life, prevent casualty’s condition from getting worse and to seek medical help as soon as possible. If you know basic first aid, you could save a life. As an employee, you are not required to provide first aid if you are not comfortable.
Flagger Orientation
Date Posted: 09/13/2016
(MUTCD Signaling & Flaggers 296-155-305 Part E)
Flaggers are to be used only when other means are not adequate to control traffic. All workers are required to have a jobsite orientation. This requirement also applies to flaggers who are working on the jobsite and any workers who will perform flagger duties. Please use MUTCD for specific requirements.
Flagging at Night
Date Posted: 09/12/2016
Night work flaggers are faced with more challenging and dangerous situations than flaggers working during daylight hours. Nighttime drivers are more inattentive due to driver fatigue from the completion of the day. It is important for flaggers to remain alert and watch traffic approaching from both directions.
Gasoline Handling Safety
Date Posted: 09/12/2016
Gasoline can be used on job-sites for some tools and equipment. Improper handling of gasoline increases the workers risk for serious injuries and even fatalities.
Geothermal Wells
Date Posted: 09/12/2016
Geo Thermal Wells can be horizontal at 5-10 feet deep but most often they are vertically drilled 150-300 feet deep into the ground. The closed loop wells are filled with HDPE pipe carrying water that leverages the earth’s constant 55 degree temperature to reduce building heating and cooling demands. The majority of the mechanical system is essentially buried underground instead of a large cooling tower and chiller. The result is a very small mechanical room, minimal wiring, materials and safety hazards after installation.
Guardrails
Date Posted: 09/11/2016
Guardrails offer a level of protection that is above personal fall arrest. When installed properly, guardrails prevent falls from happening. (WAC 296-155-24615)