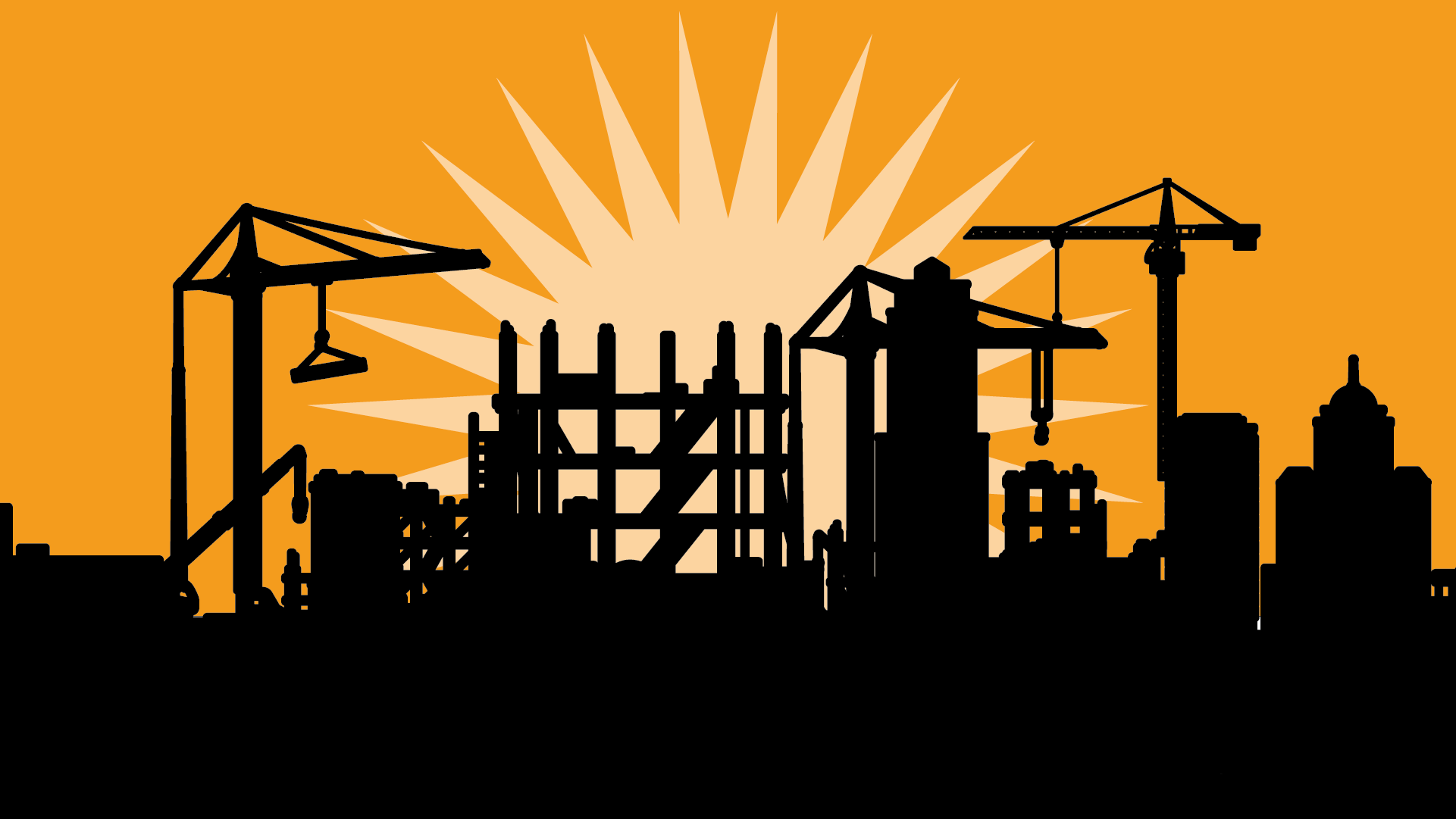
Toolbox Talks
Toolbox Talks safety briefings are an easy and efficient way to keep construction employees safe.
What are Toolbox Talks?
These brief meetings offer an opportunity for team members to learn about potential hazards and preventive measures, as well as a chance for the employer to review safety regulations. They are a great way to ensure that everyone is aware of the safety protocols that must be adhered to in order to prevent accidents and injuries on the job site.
Each toolbox talk has been reviewed and approved by a subject matter expert at L&I DOSH.
NEW! Search Toolbox Talks
Type a search term in the search box below to view English toolbox talks that match your search query. Or, use the category dropdown to view related talks.
Funding and support for the Toolbox Talks project and mobile apps has been provided by the State of Washington, Department of Labor & Industries, Safety & Health Investment Project.
Gender-Based Violence & Harassment (GBVH)
Date Published: 12/04/2024
Why is GBVH a Key Issue in Construction?
Unsafe Work Conditions: GBVH includes bullying, intimidation, sexual harassment, and other harmful behaviors, creating unsafe environments in construction workplaces.
High-Risk Situations: Women, LGBTQ individuals, and persons of color face increased risks due to discrimination, gender stereotypes, and exclusionary workplace cultures.
Gender-Based Violence and Harassment in the World of Work
Date poasted: November 25, 2024
The term “gender-based violence and harassment” (GBVH) refers to a range of unacceptable behaviors and practices, or threats thereof, whether a single occurrence or repeated, that aim to, result in, or are likely to result in physical, psychological, sexual or economic harm.
Work Zone Safety
Date Posted: 05/31/2024
According to the Bureau of Labor Statistics (BLS), there are 773 work zone-related fatalities annually. Construction workers who work on highways, roads, streets, bridges, tunnels, utilities, and other similar work for the highway infrastructure are exposed to hazards from outside and inside the work zone.
Fire Safety
Date Posted: 05/31/2024
On average, between 2016 and 2020, firefighters responded to more than 11 fires a day at buildings under construction in the U.S. Those fires led to an annual average of five civilian deaths, 62 civilian injuries, and over $376 million in direct property damages.
Construction site fires create a significant risk of property damage, personal injury, and even death.
Anchorage Selection
Date Posted: 05/31/2024
WAC 296-880-095 defines anchorage as “A secure point of attachment for lifelines, lanyards, or deceleration devices….” Insufficient anchorage strength and inappropriate anchorage connection are two common mistakes with fall protection equipment. While anchorage connectors are essential tools for keeping workers safe while working at height, they are only effective if selected and used correctly.
Lone Worker Safety
Date Posted: 05/31/2024
The term “Lone Worker” is used to describe any worker who is working remotely and without direct supervision. A Worker could be considered a lone worker at any time when their regular duties require them to work where they cannot be seen or heard by another person; they cannot expect a visit from another worker or member of the public during the ordinary course of their work; and where assistance is not readily available. While working alone is not always hazardous, it can be when other circumstances are present.
Connecting Devices
Date Posted: 05/30/2024
According to WAC 296-880-095, a connecting device or connector is “a device which is used to connect parts of the personal fall arrest system and positioning device systems together. It may be an independent component of the system, such as a carabiner, or it may be an integral component of part of the system (such as a buckle or D-ring sewn into a harness, or a snap hook spliced or sewn to a lanyard or self-retracting lanyard).
Powered Industrial Trucks (PIT)
Date Posted: 05/30/2024
Powered industrial trucks (PIT) are essential material handling tools, better known in the work environment as forklifts. PITs help save time and reduce material handling efforts when maintained and used safely. However, according to the Bureau of Labor Statistics (BLS), from 2011 to 2017, 614 workers lost their lives in forklift-related incidents, and more than 7,000 nonfatal injuries with days away from work occurred every year.
Considerations Before Excavating
Date Posted: 05/30/2024
WAC 296-155-655 requires that a competent person inspect excavations, adjacent areas, and protective systems daily for evidence of a situation that could result in possible cave-ins, indications of failure of protective systems, hazardous atmospheres, or other hazardous conditions.
Supported Scaffolding
Date Posted: 05/30/2024
According to the United States Bureau of Labor Statistics (BLS), scaffold-related accidents result in roughly 60 deaths and 4,500 injuries yearly throughout the country. Falls from scaffolds account for approximately 25% of fatal falls from all working surfaces. In the BLS study, 72% of workers injured in scaffold accidents attributed the accident to the planking or support giving way or the employee slipping or being struck by a falling object. All of these can be controlled by compliance with regulatory standards.
Step Ladder Safety
Date Posted: 05/29/2024
According to the According to Washington Administrative Code (WAC) 296-876-099 , “A self-supporting portable ladder, nonadjustable in length, with flat steps and hinged at the top. The size is designated by the overall length of the ladder measured along the front edge of the side rails.” A stepladder is a handy, simple tool, but if you do not choose the right one for the job or it is not maintained properly, you have an increased risk of injury.
Roof Work and Warning Lines
Date Posted: 05/29/2024
Roofing work can be dangerous even under the best conditions. High elevations, unprotected roof edges, and steep slopes pose fall risks. Those risks may be increased by other factors, such as wind and wet surfaces, equipment misuse or failure, particularly involving ladders, and unsafe behavior on the part of workers.
Excavations and Trenches
Date Posted: 05/29/2024
WAC 296-155-650 defines an excavation as “Any person-made cut, cavity, trench, or depression in the earth's surface, formed by earth removal.” A trench is “A narrow excavation in relation to its length made below the surface of the ground.
Incident Investigation
Date Posted: 05/29/2024
Incident investigation is determining the root causes of incidents, on-the-job injuries, property damage, and close calls to prevent them from occurring again. An incident investigation should lead you to the real cause of why something happened, and armed with that knowledge, you can take affirmative steps to prevent future incidents from occurring.
Lock Out Tag Out (LOTO)
Date Posted: 05/29/2024
The release of uncontrolled energy causes thousands of injuries each year. Each year, approximately 3,000 workers suffer lost-time injuries from being caught in dangerous parts of equipment or machinery during maintenance or cleaning, according to Bureau of Labor Statistics (BLS) data.
Concrete & Masonry Safety
Date Posted: 05/11/2024
Concrete is a common building material used regularly in the construction industry. Concrete is generally made by combining cement, sand, aggregate (small stones), and water.
Extension Ladder Safety
Date Posted: 05/11/2024
Although one of the most common tools used on a construction site, extension ladders can lead to severe injuries or even fatal incidents if improperly used. Ladders are involved in 20 percent of fall injuries among workers and 81 percent of construction worker fall injuries.
Flagger Hazards
Date Posted: 05/11/2024
Flagging traffic is both a critical and a potentially hazardous part of providing a safe work zone for workers, the general public, and motorists. According to an OSHA Fact Sheet, “transportation incidents and workers struck by vehicles are responsible for the highest number of fatal work injuries,” according to data from the Bureau of Labor Statistics.
HAZCOM – Understanding Chemical Labels
Date Posted: 05/11/2024
In 2012, the Occupational Safety and Health Administration (OSHA) revised the existing Hazard Communication (HAZCOM) standard and aligned it with the United Nations (US) Globally Harmonized System (GHS). The GHS includes criteria for the classification of health, physical, and environmental hazards, as well as specifying what information should be included on labels of hazardous chemicals and safety data sheets.
Hearing Protection
Date Posted: 05/11/2024
According to the National Institute for Occupational Safety & Health (NIOSH), approximately 22 million workers yearly are exposed to hazardous work-related noise. As a result, occupational hearing loss is one of the most common work-related illnesses in the U.S.
Download the FREE
Toolbox Talks App!
Discover, discuss, and document over 150 Toolbox Talks! The Toolbox Talks app makes it simple to find safety talks for both construction and marine industries in English, Spanish, and Russian. Find a talk to review, then document your safety briefing with a signature capture form that generates a PDF of the meeting details that you can email or save to your device.
Funding and support for the Toolbox Talks project and mobile apps has been provided by the State of Washington, Department of Labor & Industries, Safety & Health Investment Project.